Innovating through recycling: 3D printing and circular economy in healthcare
3D printing is transforming the healthcare sector, unlocking new possibilities for creating personalized medical devices and patient-specific anatomical models. However, integrating circular economy principles – especially effective plastic recycling – into innovation processes remains a challenge.
A study led by Paolo Oliva – Head of Research Technology Management at Humanitas and the 3D Innovation Lab – addresses this gap. The lab, a joint initiative between Humanitas University and the IRCCS Istituto Clinico Humanitas, fosters the cross-pollination of clinical practice, scientific research, and academic training through the development of innovative 3D printing solutions.
The study, published in Frontiers in Bioengineering and Biotechnology, demonstrates the feasibility of a sustainable and low-cost 3D printing supply chain using recycled hospital plastic – starting from common plastic bottle caps – to produce high-quality filaments.
Transforming plastic: the path to 3D filament
“The project explores the recovery of high-density polyethylene (HDPE) caps from hospital environments. The transformation process, including collection, shredding, extrusion, and spooling, has been optimized to produce a homogeneous filament with good mechanical properties suitable for clinical applications. Each step was fine-tuned to ensure consistent output and high-quality final material,” explains Nada Mansour, a bioengineer at the 3D Innovation Lab and lead author of the study.
Beyond the technical aspects, the study evaluated the economic and environmental impact of the process. “The results revealed a significant cost reduction compared to purchasing commercial filaments and a decrease in CO₂ emissions, making this approach a viable alternative to traditional materials,” says Paolo Oliva. “This initiative demonstrates that plastic waste, when properly treated, can be reintegrated into the 3D printing supply chain with tangible benefits.”
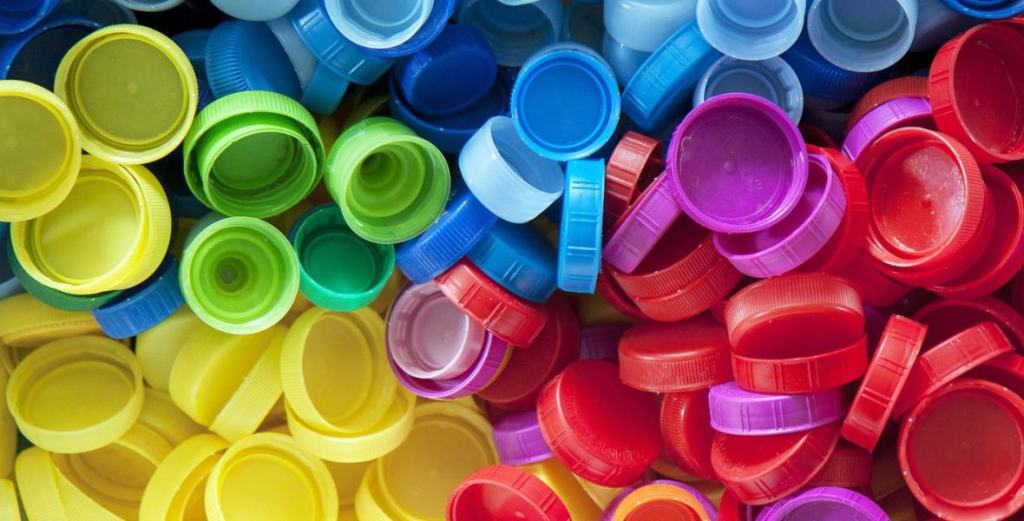
Clinical Applications
One of the most significant outcomes was the use of recycled filament to print a customized anatomical model of an intracranial aneurysm, utilized in surgical planning. This case confirms the potential for recycled materials to be employed even in high-precision clinical contexts without compromising product quality or functionality.
The study conducted at Humanitas highlights how the combination of 3D printing, material recycling, and technological innovation – actively promoted by the 3D Innovation Lab – can make the healthcare system more innovative and sustainable. “Integrating circular economy practices not only reduces environmental impact but also opens new opportunities for smart resource reuse and personalized treatments,” concludes Oliva.